Sustainability
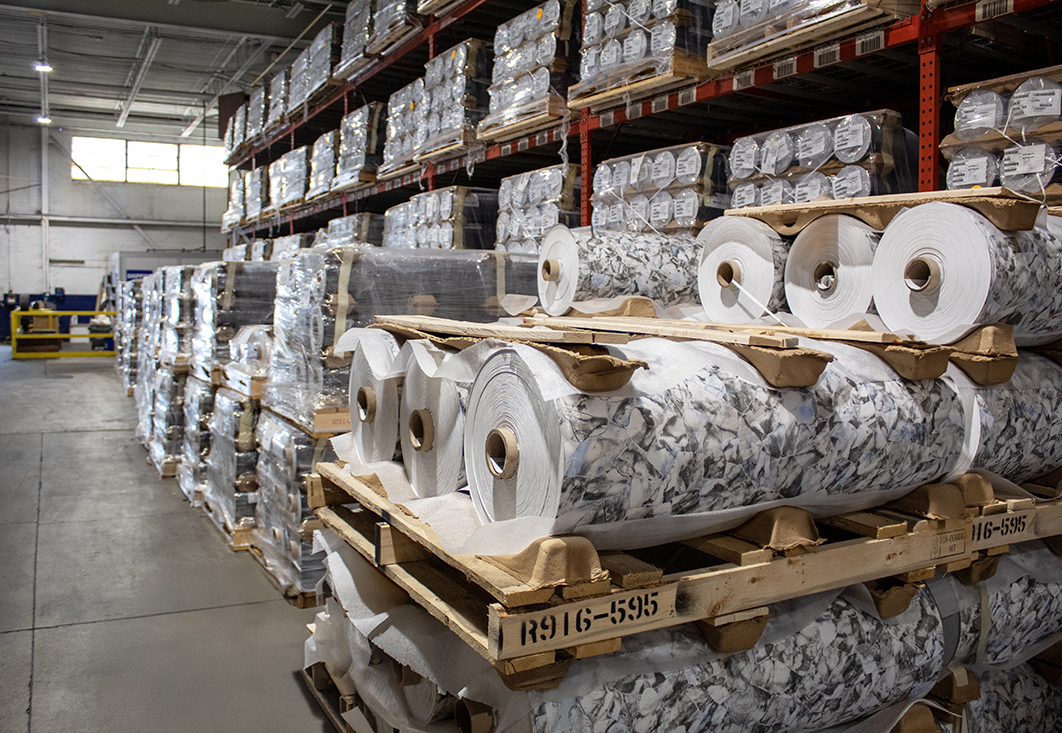
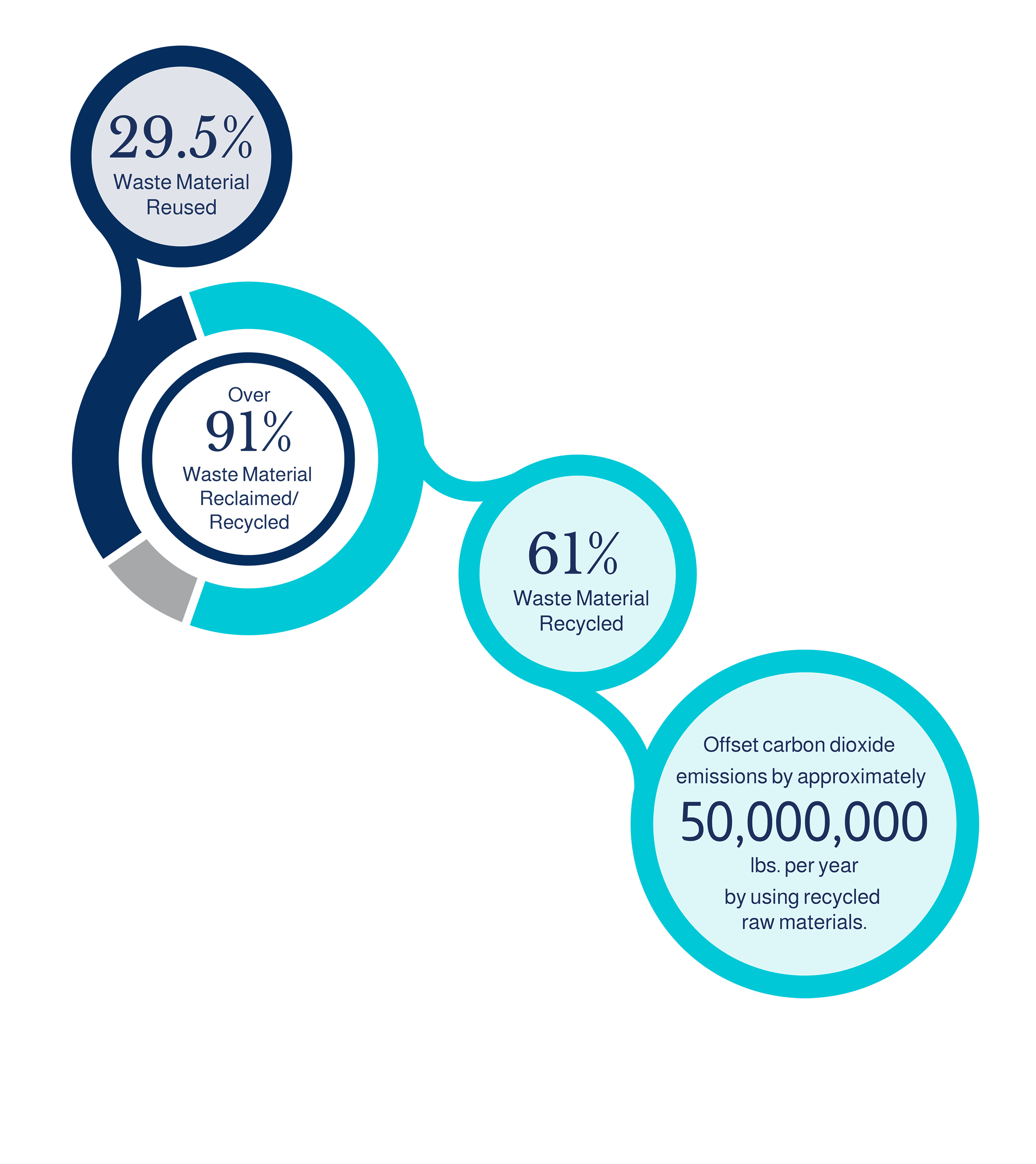
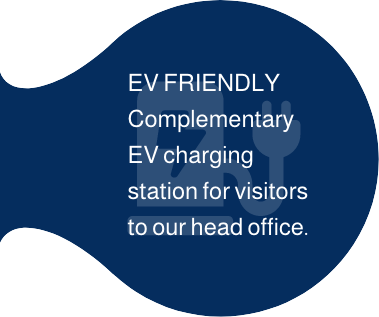
Investing in
Sustainable Technology
In the past 5 years, CGT has invested millions of dollars in air pollution control technology at our manufacturing sites in China, North America and Europe. Such as investments in Regenerative Thermal Oxidizers (RTOs), plasticizer recovery units, and activate carbon towers, in order to reduce hazardous air emissions by 90%. To allow for real-time monitoring and optimizing of utility consumption CGT has installed SCADA systems. This will allow us to further reduce 0.05lbs of carbon dioxide emissions for each yard of polymeric film produced by CGT by reducing usage of electricity, natural gas, and water. In addition CGT’s facilities are commissioned with the forethought of a low electricity consumption using high efficiency LED lights automatic timers and motion detectors.
CGT Sustainability
Sustainability is a part of CGT’s backbone strategy in our company’s history of more than 150 years in business. Since the 1920’s CGT has had a solid record of providing solutions to meet the requirements for improved recycling of industrial scraps and reduced industrial production waste disposed to landfill, as well as developing and implementing products with high sustainable content.
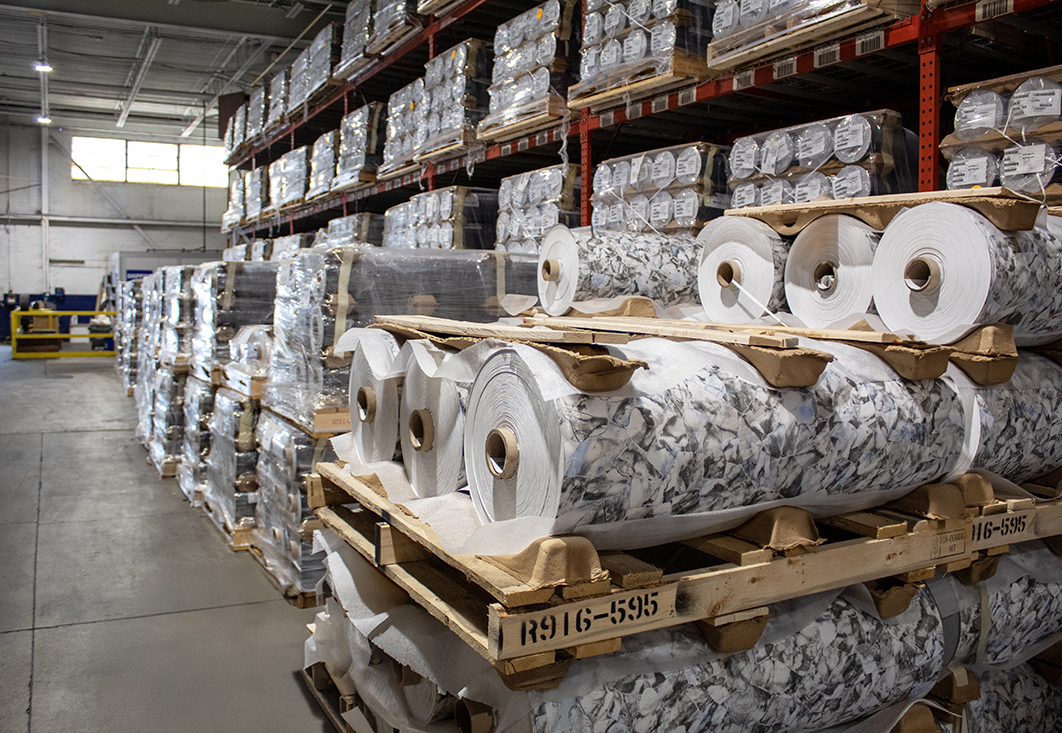
A History of Sustainable Manufacturing
CGT is committed to reducing our carbon footprint and conserving energy usage through sustainable manufacturing processes. CGT pioneered vinyl recycling processes that are a key part of our environmental sustainability efforts. In 2000, CGT became the first vinyl manufacturing facility in North America that was registered to ISO 14001. CGT’s global presence includes multiple manufacturing facilities that are certified to comply with ISO 14001 Environmental Management System and ISO 45001 Occupational Health and Safety Management System.
Sustainability Roadmap
Today CGT reclaims/recycles up to 3 million KGs of PVC each year at our Cambridge facility. In fact, >91% of production waste material from CGT’s Cambridge operation is reclaimed/reused for industrial product applications, far exceeding the federal and provincial target for landfill diversion rates. This means that CGT offsets the carbon footprint of our production by about 50 million lbs of carbon dioxide emissions per year.
Sustainability Roadmap
Today CGT reclaims/recycles up to 3 million KGs of PVC each year at our Cambridge facility. In fact, >91% of production waste material from CGT’s Cambridge operation is reclaimed/reused for industrial product applications, far exceeding the federal and provincial target for landfill diversion rates. This means that CGT offsets the carbon footprint of our production by about 50 million lbs of carbon dioxide emissions per year.https://www.cgtower.com/industrial/
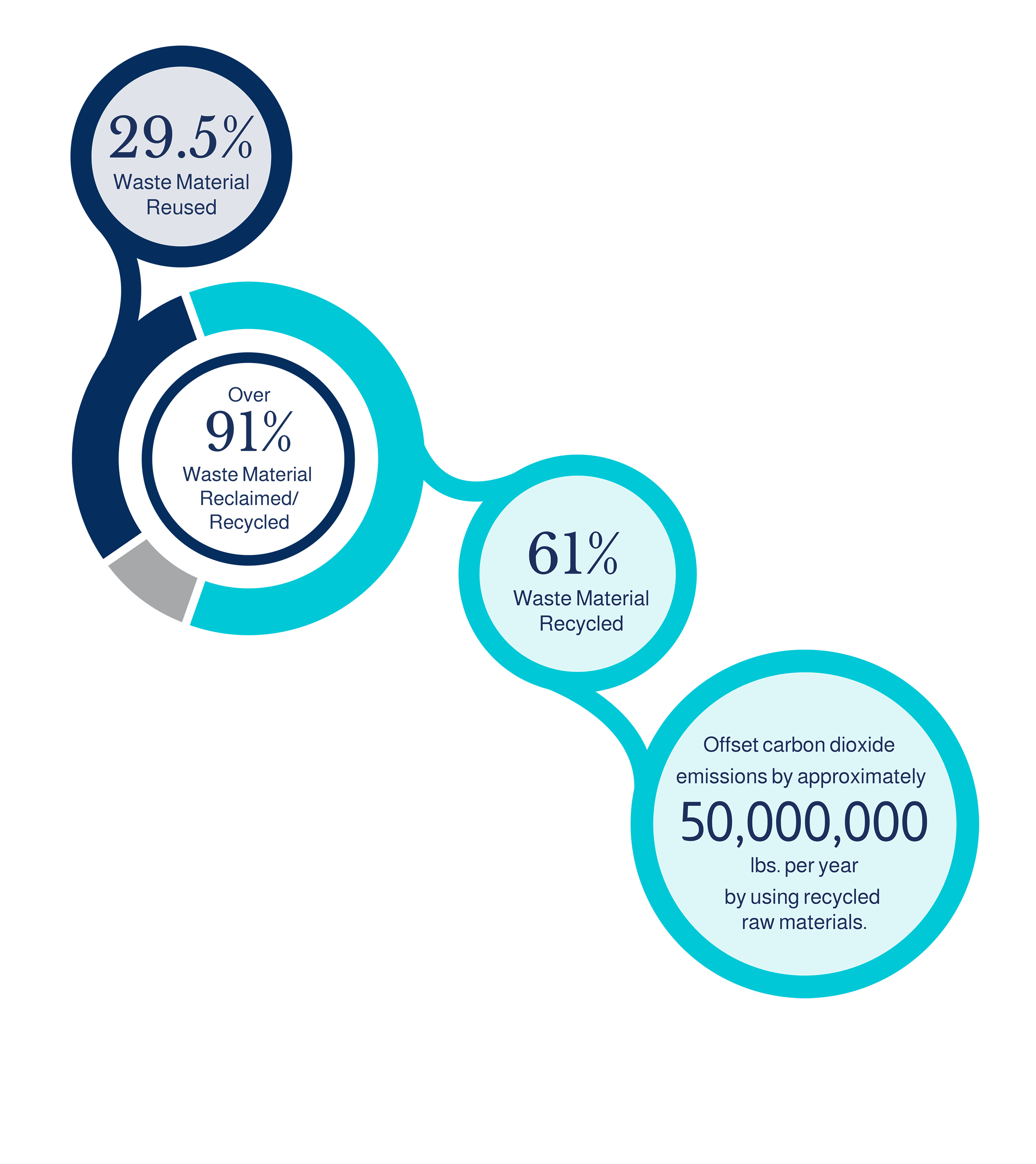
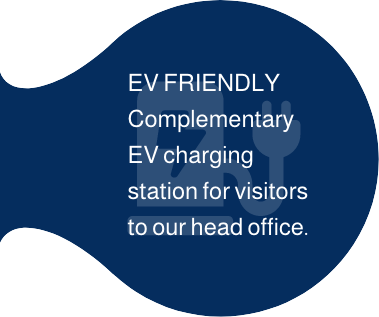
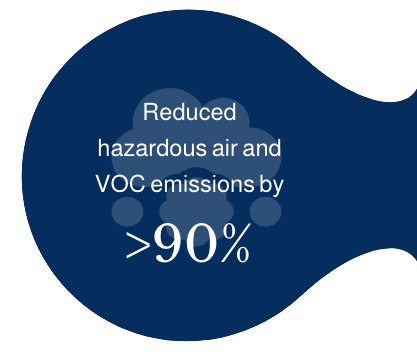
Investing in
Sustainable Technology
In the past 5 years, CGT has invested millions of dollars in air pollution control technology at our manufacturing sites in China, North America and Europe. Such as investments in Regenerative Thermal Oxidizers (RTOs), plasticizer recovery units, and activate carbon towers, in order to reduce hazardous air emissions by 90%. To allow for real-time monitoring and optimizing of utility consumption CGT has installed SCADA systems. This will allow us to further reduce 0.05lbs of carbon dioxide emissions for each yard of polymeric film produced by CGT by reducing usage of electricity, natural gas, and water. In addition CGT’s facilities are commissioned with the forethought of a low electricity consumption using high efficiency LED lights automatic timers and motion detectors.
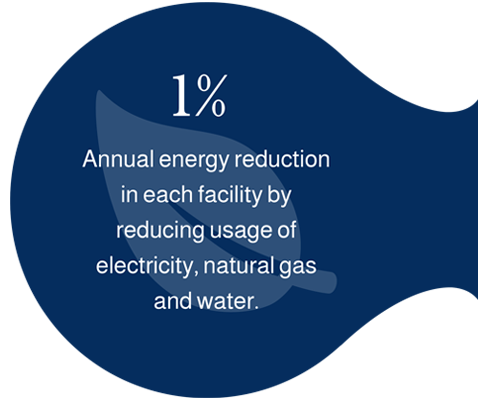